B/stationary asphalt plant “Teltomat-80” 2003
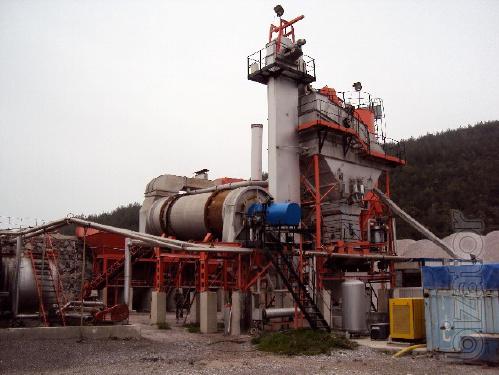
Company: | SUMAB Ukraina |
Seller: | ![]() |
Phones: | ![]() +380507383348 Show phone |
Address: | Ukraine |
B/Stationary asphalt plant "Teltomat-80”, 2003, V. (Germany)
Parameters :
Production date : 2003
Replacement of computer system : 2017 (New control system)
Full maintenance of the plant : 2017 (cap. repair)
Standard conditions of production and the characteristics of the plant:
This asphalt plant is designed for production of hot asphalt mixtures 80 tons / hour humidity 3% and temperature of finished product of 160 ° C.
- The combined ratio % 3
• The supply temperature of the unit in the dryer for more than 10 º C
• Operating altitude: sea level
• Approximately unit density of 1,650 kg / m3
• Fuel oil no: 6 calories 9,200 kcal / kg
• Fuel oil no: 4 caloric value 9,700 kcal / kg
• The value of diesel calories 10.200 kcal / kg
• Calorific value of natural gas 7,600 kcal / kg
• The temperature increase Δt of the heated to 160 K
• Coefficient of wetness of the mixture,% 0,3
• Max. The aggregate grain size of 40 mm.
• The fill factor of the mesh grid 3 mm% 35
• Material-80 µm from the vibration absorber % 8
• The total specific heat% of 0.21 kcal / kg º C
• Production capacity includes all the number of fillers collected from the filter and % 5 bits. weight
• The material should be of cubic shape, and inside it should not be irregular in shape and debris.
• Production capacity can be adjusted depending on the ambient temperature variants, i.e. ± 10%
Technical specification :
1.0 supply System of cold aggregate
1.1. 4 x 12 m3 hopper of aggregate material
1.2. 4 pieces Dosing conveyor (frequency control, new gear motor)
1.3. 1 PC Central conveyor feeder (L: 16.000 mm W: 500 mm)
1.4. 1 Corner conveyor (L: 11,500 mm, W: 500 mm)
1,5. 1 Vibrator (hopper with sand)
2.0 Dryer and burner.
2.1. Tumble dryer
2.2. Oil and diesel burner (Benninghoven Brand)
2.3. Fuel heating (Brand Benninghoven, Electrical)
2.4. Temperature sensor Assembly
3.0 filtration System
3.1. Cleaning system (rail type) (main unit)
3.2. The preliminary separator, a primary dust and gas channel
3.3. Exhaust fan, a flue and a dust channel
3.4. Screw conveyors for fine and coarse filler
4.0 vibrating screen, mixer
4.1 Hot Elevator
4.2 Shielding unit (4 sections)
4.3 hot Bins Assembly (4 section)
4.4 load cell and electronic weighing system
4.4.1 Aggregate weighing (Capacity: 1000kg)
4.4.2 Weighing filler (Capacity: 200 kg)
4.4.3 Weighting of bitumen (capacity: 150 kg)
4.5 Mixer (Capacity: 1000 kg/batch)
4.6 Platforms and stairways
4.7 Pneumatic system compressor
4.8 the control Cabin and computer system
4.8.1 the control Cabin
4.8.2 power Panels and control
4.8.3 Fully computerized control system
5.0 Storage of mineral supplements and feed system.
5.1 1 tank of 30 m3 filler
5.2 1 PC filler
5.2 1 PC. Feeding screw conveyor (bunker-vzveshivat)
6.0 supply System of bitumen and thermal oil.
6.1 Device for weighing the bitumen
6.2 250.000 - kCal / hr Thermal oil heater
6.3 2 pieces of 40 m3 Bitumen tank
6.4 1 EA. of 30 m3 Fuel tank
Plant in excellent working condition.
Overhaul-maintenance with replacement of worn parts.