Concrete factory SAT-M performance BSU 80 m3/h
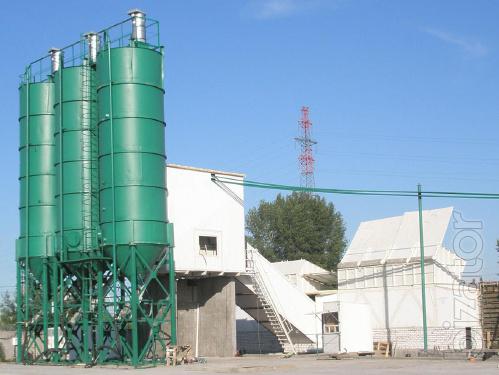
Price: | negotiated |
Company: | Mashinostroitel'nyij zavod PAO 'Betonmash' |
Seller: | ![]() |
Phones: | ![]() |
Address: | Ukraine, Donets'ka Oblast', Sloviansk |
PJSC "buttonmash produces and delivers fast, does not require
special foundations mixing plant SB-N
performance 80m3/hour on the surface of the concrete (winter version).
The latest development engineering and design services plant
concrete batching plant SB-N is designed for the production
different types of concrete mixtures at construction sites when
the ambient air temperature from-200C to +400C.
Technical characteristics of the concrete mixing plant:
The number of fractions and the amount of placeholders :
1st option - four fractions of inert 4 x 18 m3 (total t)
2nd option - three fractions of inert 3 x 18 m3 (total t)
The number of feed bins and the amount of binder (cement) - 3 x 85 m3 (total t)
The type of mixer is twin-shaft forced actions, cyclic BP-2G -300
An upper bound and a batching error:
batcher inert materials kg / ±2%
batcher, cement kg / ±1%
- water dispenser kg / ±1%
- dispensers concentrated khimdobavki 40 kg + 10 kg / ±1%
Installed motor power 180 kW
Working air pressure in the pneumatic system 0.6 MPa
In the design of the facility using high quality components and
components from the best manufacturers gear
the mixer, steeply inclined conveyor and screw feeders
Italian firm "Bonfigliolli"; a gear motor belt feeders
MTS (Czech Republic); all dispensers are made with reliable strain measurement European
manufacturers; pneumatic installation, gate, valve, pointers
levels are made on the basis of the leading Italian manufacturers of firms "Wam" and
"Camozzi".
To reduce the time of installation and commissioning works on starting
the operation of the concrete batching plant made in block
the execution, while the blocks have higher availability. In each block
are all the main actuators and devices
terminal power cable and pneumothrax. Feature
installation is articulated metal frame block
mixing, which is integrated with the gallery belt conveyor,
which also facilitates Assembly / disassembly installation.
Download bunkers inert expected with ramps height of not more than
1.8m front end loader with the width of the bucket to 3.2 meters output
mouths bins installed air-actuated jaw closures (2
for each section) through which is inert in the dispenser
according to the "rude". Each compartment is equipped with a vibrator for
improve the expiry of the material. Hopper inert in the 1st version
picking placed on both the side perpendicular to the axis inclined
conveyor, and in the 2nd variant - axis of the conveyor.
Tract inert materials includes two dispenser inert
(in the 2nd variant - one dispenser), made on the base tape
conveyor with belt width 800 mm and suspended on 4 load cells
each. Supply of aggregates is carried out by using an inclined
belt conveyor with ribbed belt width 1000 mm with cleaning
the brush device of the tape. Drive pulley conveyor - rubber
(rubber).
Warehouse cement consists of three tanks FMM on tn each with
bag filters with the system of compulsory Vibroscreen,
indicator level ILТCO (Italy), with aeration and pneumovirinae
cone parts silos. The cement is loaded into the feed hopper
is the cement trucks with pneumography (or
on-site warehouse with cement pumping devices). At the bottom
parts bins installed manual gate valves exhaust openings.
Supply of cement in the cement batcher is inclined screw
feeders with a screw diameter of 300mm.
The mixing unit, including high-performance, twin-shaft
concrete mixer BP-2G-3000/2000, allowing to obtain a homogeneous
the concrete mix for 30 seconds, stirring. The mixer is equipped with
forced lubrication system seals the mixing shaft pressure
300 bar, with soft starters drives. As drives
used planetary gearbox Italian firm "Bonfigliolli",
widely used counterparts from leading European manufacturers.
The capacity of the installed motors - 2 x wt. Under the block
mixing set discharge hopper with a capacity of 2 m3. In block
provided with forced aspiration system, which includes
himself filter and exhaust fan. Over the faucet elastomers,
excluding additional error from vibration, compact
installed in unit dosage dosage of cement and water, integrated
with the lid of the mixer in one Assembly unit. Water for cooking
concrete tank (Customer supplied) a pump dispenser
water.
The equipment is made on the basis of elements of Italian firms
"Camozzi" (pneumatic cylinders, pneumology, including pneumatic,
valves, gauges, fittings).
The control unit is the operator of freestanding
comfortable cabins, with power enclosures of electrical equipment, including
smooth start mixer, frequency converters,
machines, switchgear and control panel with microprocessor system
control, controller and mnemonic, air conditioning system
space heating. The unit is equipped with a video monitoring system
the operation of the mechanisms and process of the finished mixture in the transport and
includes 4 cameras and a monitor with simultaneous
observations immediately for all objects.
The mode of operation BSU - automatic, semi-automatic, adjustment, with
the use of microprocessor control systems "Mix Master" on the basis of
industrial computer (PC) software, which
enables password management access, visualize
technologists