Technical Supplement in casting ASG
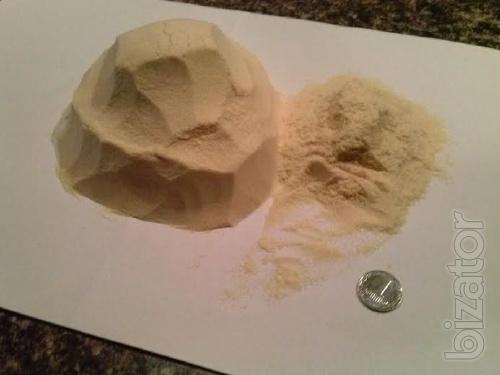
Price: | negotiated |
Company: | MIK-KORN |
Seller: | ![]() |
Phones: | ![]() 0932878320 Show phone |
Address: | Ukraine, Cherkas'ka Oblast', Cherkasy |
Extrusion of starch-containing reagent (SCR, SCR, Cromalin)
In foundry castings are produced in wet sand and clay forms, which are characterized by their pouring metal to collapse with the formation of characteristic defects: Weimin, clogs, sand and gas shells.
To increase the stability of the raw sand and clay forms against defects technological additives are used, in particular the SCREEN, which halogenase starch.
A similar SCREEN is kromadit, which is different from the Screen for feedstock from which it is made. The appointment SCREEN and bromalite the same. Everything stated in this article regarding the SCREEN, remains fully valid and bromalite.
The total content of the Screen in the sand should be: for cast iron is 0.3% for steel castings - 0.4% by weight of the mixture. However, in one cycle the whole mass of the Screen does not fade. His frenzy for one cycle is about 15-20% of the total content of the Screen in the composition of the sand-clay mixture (hereinafter CBA). Therefore, when the content of the Screen in the molding compound has stabilized at a level of 0.3% for iron and 0.4% for steel castings, adding Screen in each batch of the mixture should on average be: for cast iron and 0.06%; for steel castings to 0.08% by weight of the mixture.
SCREEN - fine powder . He is introduced into the mixture together with other loose materials (sand, clay).
When established technology, when there was already a saturation of the moulding mixture of the Screen to the above limits its consumption with the average consumption of 5 tonnes ASG 1 t casting is: for cast iron 3 kg for steel 4 kg per ton of castings. It is known that loss of marriage when using CBC without Screen many times more cost on the SCREEN.
Thanks to the Screen eliminates this disadvantage ASG, as conquest. The mixture becomes friable, slightly granular, still it is good to be condensed and to acquire a higher density.
The most important technological characteristic of sand, through which manifests the positive effect of the Screen is the hardness of the compacted form, as measured by a Durometer.
One of the positive effects of the Screen lies in the reduction of internal friction due to the absorption of moisture by krahmalom. As a result, the sand formed a jelly-like bisokotuwa weight consisting of water, swollen with the absorption of water Full and hydrated bentonite. This mass facilitates mixing of the grains relative to each other. Microresonator this is to increase the hardness and strength of the sand due to its better seal.
The effectiveness of the Screen in the calibration gas depends on many factors, which include, in particular, is the content of the pulverulent fraction consisting of the following components:
·Annealed (emotitionaly) clay ballast and the most harmful for the quality of the casting component. She is not involved in the formation of raw strength, clogs the pores in the ASG, reduces its permeability, impairs nonstick properties and increases its tendency to form blockages, Weimin and sand wash basins.
·Active (i.e., unfired) clay, which is involved in the formation of raw strength CBC gives it flexibility, fluidity, and formability.
·Fine fraction of sand resulting from the cracking of larger sand grains under the action of the molten metal and friction.
·Graffitistyle materials (from separating coatings, powders, Pribylov).
·Toxic resulting from thermal decomposition of organic binders, oils, kerosene separation of coatings and other
The above components are present in the ASG collectively and mutually mixed state.
After readjustment of the calibration gas must be regularly refreshed, adding 10-15 % quartz sand; 1-2% of bentonite and 1% lignosulfonate technical liquid. As a result, the composition of the calibration gas shall be as follows, %:
·Waste mixture 85-90
·Quartz sand - 10-15
·Activated bentonite - 1-2
·Screen: for cast iron - 0,06; for steel castings - 0,08
·The technical lignosulphonate liquid - 1,0
Thus the physico-mechanical properties of PGS will be:
Source data:
·σсж - to 1.0 kgf/cm2
·Humidity - 3.8
·Permeability - 140 units
·Fluidity - 39 %
With the addition of SCR (Bromalite) (reagent production MIK-KORN):
·σсж - to 1.1 kgf/cm2
·Humidity - 3.6
·Permeability - 220 units
·Fluidity - 71 %
It is very important not to allow a higher humidity calibration gas, as this may lead to a decrease σсж and education Weimin, clogs, sand and gas pockets in the casting.
In conclusion, we can state that the most important means of combating WikiName and clogging is moderate humidity, good air permeability ASG (not less than 100 units) and uniform seal.